Производство
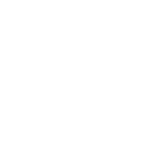
Разработка моделей строится на аналитике большого количества информации разных направлений развития текстильных материалов, технологий, оборудования, дизайна, покупательского спроса. На основании этого разрабатывается стратегия развития коллекции.
Важным этапом разработки изделий и коллекций является грамотный подбор комплектующих. Работа ведется с десятками поставщиков тканей и фурнитуры. Отбираются перспективные образцы, которые проходят полноценный цикл испытаний на фабрике и оценивается их пригодность для внедрения в коллекции. Как правило, в коллекцию проходят материалы, являющиеся лидерами в своем классе по функциональным свойствам и качеству. Нередко для качественного подбора основных комплектующих, вроде мембранных материалов и утеплителей проводятся НИОКР на базе испытательной лаборатории на фабрике.
Готовый прототип подвергается полноценному анализу и проверке соответствия техническому заданию.
После примерки и выявленных замечаний, как правило, прототип отправляется на полевое тестирование. По результатам этих испытаний и анализа замечаний производится доработанное изделие, после чего модель окончательно утверждают и начинают подготовку к запуску серийного производства.
В нашей работе мы предъявляем высокие требования ко всем составляющим процесса производства. Особенно тщательно подбирается оборудование, которое мы используем при создании одежды и снаряжения. Главными параметрами при выборе являются качество, скорость работы и надежность. Зачастую всем этим требованиям отвечают только самые современные модели производственных машин.
Процесс раскроя материалов - это долгий, трудоёмкий процесс, требующий большой точности и немалого опыта от мастеров производства. На нашей фабрике мы используем автоматический раскройный комплекс нового поколения, который позволяет с максимальной точностью изготавливать детали кроя со значительной экономией времени, по сравнению с ручной резкой. Тем не менее, резка деталей кроя из некоторых сложных материалов может быть выполнена только руками опытного мастера.
Автоматизированная вышивка исторически является самым надёжным и красивым методом нанесения символики на изделия, так как она не боится воды и устойчива к ультрафиолетовому излучению, не теряет своего внешнего вида и остаётся привлекательной в течение всего срока службы изделия.
Лазерное оборудование позволяет выполнять точный крой мелких деталей, предназначенных для последующего термического нанесения на изделия усилений, функциональных элементов и логотипов, а также производить гравировку на поверхности тканей.
Преимущества:
- отсутствие проколов от иглы на месте шва;
- высокая прочность шва;
- абсолютно плоский шов;
- полная герметичность шва;
- отсутствие миграции пуха в пуховых изделиях, защита пуха от намокания.
Несмотря на высокую трудоёмкость бесшовных операций, которые выполняются с помощью специальных прессов и герметизирующих машин, эта современная технология проникает в технологические процессы и занимает все больше и больше места в сборке и отделке изделий.
Несмотря на активное развитие бесшовных технологий, швейное оборудование также не стоит на месте и постоянно развивается. Современные машины становятся более функциональными, точными и быстрыми. Больше операций выполняются с минимальным участием человека.
Автоматизация - один из главных трендов в легкой промышленности, но сложная нестандартная экипировка outdoor не позволяют добиться высокой степени автоматизации производства. Пока преобладает и высоко ценится ручной труд квалифицированных швей.
Помимо оборудования и опыта работы также важны и комплектующие. Грамотный подбор ниток позволяет улучшить качество изделия: повысить надежность, комфорт эксплуатации, улучшить посадку и даже защитить от проникновения внешней влаги.
Автоматизация процесса набивки изделий пуха позволяет получать высокую точность дозирования и производительность. Практически исключена возможность нарушений плотности набивки в сравнении с ручным методом.
Многосутпенчатый контроль качества является фундаментом успешной работы по производству высококачественных изделий. Три основных уровня контроля качества на нашей фабрике:
- входной контроль всех комплектующих (тканей, утеплителей, фурнитуры);
- межоперационный контроль на всех этапах поузловой технологической сборки изделий;
- контроль готовых изделий.
Существенно снижает затраты и повышает производительность труда на швейном производстве автоматизация производственных процессов, что неизбежно благотворно сказывается на себестоимости изделий. На нашей фабрике частично или полностью автоматизированы процессы:
- конструирования изделий;
- написания технологических процессов;
- подбора технологического оборудования и оснастки;
- ведения складского учета комплектующих и готовой продукции.